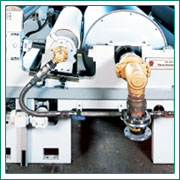
Process
Coating: In the extrusion coating process resin like polyethylene, ethylene vinyl acetate copolymers and polypropylene are melted and formed into thin hot film. The extruder has the ability to convert the solid resin uniform melting liquid. Commonly, flat type dies with adjustable die lip are used. The melt resin flow through the die which is made of chilled roll and back roll. The large diameter formed, allow the resin to cool and to form the film plastic strip.
The plastic strip is coated on moving flat substrates like paper, paper board, metal foil and plastic film. Coated substance then passes between a set of counter rotating rolls which press the coating onto the substrate to ensure complete contact and adhesion. The surface of the chilled role may be bright, dull and embossed depending on the desired surface characteristics.
Lamination: Extrusions lamination is a process that is used to combine two different materials like molten polymers. Also known as sandwich lamination, this process is similar to the extrusion coating process but for the fact that the extrusion coated layer is used as an adhesive layer between two or more substrates. A secondary layer is applied to the extrusion coating while it it still hot. The sandwich is then pressed together by pressure rolls. The Extrusion lamination are done commonly using plastic, but metals and paper can also be used. Lamination of different thickness with various levels of quality of lamination and coating can be produced.
Factor that effect plastic coating process: Numerous factors determine the quality of the extrusion coated and laminated product. Some of the important factors being:
Temperature: Melt temperature greatly influences the quality of coating. When the resin is heated at higher temperature, the polymer is oxidized, that promotes good bonding between the polymer and the substrate.
Die Gap: The higher the die gap, the greater is the flow variation of the polymers.

Air Gap: Air gap is the gap that exist between the die die exit and the chilled roll. If the gap is big, the adhesion between the polymer and the substrate will be improper due to high necking and cooling of the melt.
Nowadays, sophisticated range of machines are available in the market that are durable,productive and can be used for both laminating and coating purpose. Some coating machines are available with coating width of 3 feet to 16 feet, allowing coating and lamination thickness that can vary depending on the end usage.
Application
Plastic extrusion coating lamination plant are used for a variety of applications like:
- Woven sacks for fertilizer packaging
- Tarpaulins
- Coatings on conventional jute bags
- Pharmaceutical strip packaging
- Cable wraps
- Coating on paper
No comments:
Post a Comment