Most polymeric materials are extruded at least twice in their lifetime, rst through a pelletising die after the reactor and then for nal shaping.In simplest terms, screw extruders are polymer pumps with the capacity to melt the material which they are fed. Screw extruders comprise one or two Archimedean screws rotating in a heated barrel.
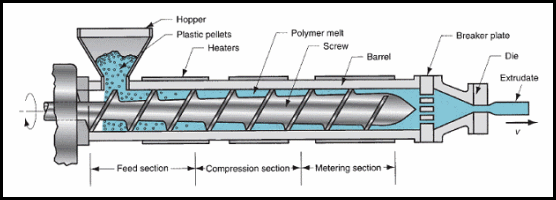
The single screw extruder (SSE) is the workhorse of the plastics industry. Polymer resins in the form of pellets, powders or fakes from a hopper to the gap between a rotating screw and a heated barrel. The depth of the con- veying channel in the screw is contoured from large to small in the ow direction, to account for the density change from the particulate solid feed to the molten polymer extrudate, and for pressure development. The SSEs normally have diameters between 25 and 250 mm, and length/diameter ratios between 20 and 36. Usual rotation speeds range from 20 to 150 rev min . A 60 mm diameter machine may deliver up to 200 kg , while a 150 mm diameter machine can exceed 1000 kg.
In the first, or solids conveying, zone of the extruder, the solid polymer particles are compacted together in the screw channel by the rotating action of the screw to form a solid bed of material.At the start of the next extrudersection, the plastication (melting) zone, barrel heaters cause a thin film of molten polymer to form in the gap between the solid bed and the barrel wall. The melt lm is subjected to intense shearing in the thin gap, and because of the extremely high viscosities of molten polymers, high rates of viscous dissipation result. The generated heat melts the solid bed within a short distance of the start of melting. In the last zone of the extruder, the metering section, the polymer melt flow is stabilised in the shallow screw channels, and nally the material passes out through the die at the end of the machine.
Pressurebuildupowing to frictionalforcesin the solids con- veying section of the screw has been modelled by Darnell and Mol (along with some more recent research ) on the basis of force and torque balances, which result in an exponential expression. For forward motion of the solid bed, the friction coeffcient must be larger on the barrel than on the screw. Screws have polished surfaces. The barrel surfaces are sometimes intentionally roughened (as in grooved barrels).
No comments:
Post a Comment